You may not always be aware of it, but cement is nearly everywhere: in the houses we live in, the foundations they stand on, the roads we use and the bridges we cross. It is one of the most consumed products globally− second only to potable water. But did you know it also accounts for a quarter of all industrial CO2 emissions and 5% of human greenhouse gas (GHG) emissions? As global development steadily carries on, demand for cement is soaring, threatening our climate goals. We will need a multi-faceted approach to decarbonize cement and the building industry. Tech startups, governments, powerful incumbents and climate investors all play a vital role. Let’s find out how!
A concrete challenge
We are amidst human history's biggest wave of building and infrastructure growth. Three-quarters of the infrastructure that will exist in 2050 has yet to be built, and we will have added 230 billion m2 of new construction to our global building stock by 2060. This is equivalent to constructing a city the size of Paris every week! The building and use of all this new infrastructure are estimated to release a massive amount of CO2 into the atmosphere: more than half of our remaining global carbon budget if we want to have a 50% chance of limiting global warming to 1.5°C.
To create concrete, we need cement, a substance that binds sand or crushed stone together. Cement production requires an immense amount of energy: it makes up only 12% of the volume of the concrete mix but is almost solely responsible for the CO2 emissions of the material. Overall, producing one kilogram of cement releases an equivalent amount of CO2 into the atmosphere.
This has proven to have quite the impact: The cement industry generates about 25% of all industrial CO2 emissions and 5% of all human greenhouse gas emissions.
Cement as a carbon source
So why is cement production this carbon-intensive?
Portland cement is the most common type of cement, and its production process for this type has been the same for a century. Crushed limestone (calcium carbonate, or CaCO3), clay and sand are heated in large cement kilns, which convert them first to quicklime (calcium oxide, or CaO), which binds with components from the clay and sand, and eventually turns into clinker nodules. The clinker is then ground to a fine powder, serving as the binder in cement products. This complex production process includes two primary sources of CO2:
- Fuel combustion (40%) The kilns heat the material to temperatures up to 1450°C. The type of fuel that is used for this directly impacts the CO2 emissions from these installations. Currently, they are predominantly fueled by coal or petcoke.
- Calcination reaction (50%) The conversion of limestone to quicklime happens through calcination, a chemical reaction. This reaction inherently produces CO2 as a byproduct, meaning this carbon source is unavoidable in the current production process.
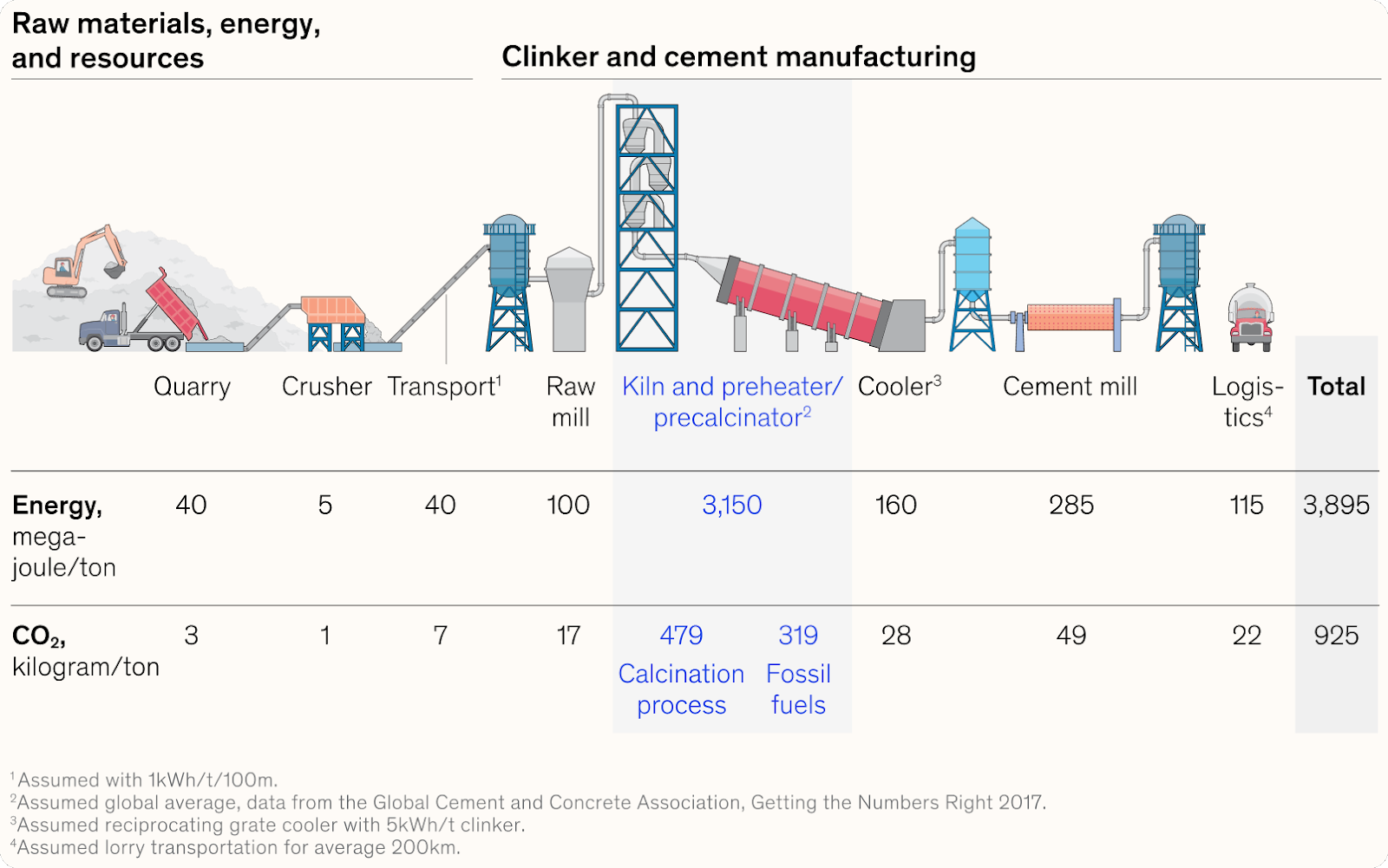
The last source of CO2 emissions is the transport of cement and the electricity used in production, which together account for 10% of emissions.
How do we solve this?
Disrupting the conservative cement sector is challenging. The capital requirements are high, the end product is commoditized, and the existing technologies and markets have huge amounts of embedded infrastructure and complex supply chains.
We can reduce cement emissions by 75% by 2050 and possibly even achieve zero emissions from concrete thereafter, but the tech we need for this is still in early development stages. Next to that, as there are many types of concrete that we use, there is no one-size-fits-all solution to decarbonize them all, so we’ll likely need a myriad of solutions to get to zero. After all, emissions originate from different sources, there are many types of cement and even more applications for them. This means that technologies that improve or replace cement as a product cannot do the job by themselves. We will need a comprehensive, multi-faceted approach that combines measures on the demand and supply side, which should both be supported by policies and complemented by tech.
Reducing emissions on demand
The first intervention is reducing demand for cement altogether, a measure that cuts emissions from both aforementioned primary CO2 sources. We can reduce cement demand in roughly two ways:
1) Changing how much we use when we build
Material-efficient design has great potential to reduce emissions, while traditional design mainly focuses on reducing costs. Simultaneously, lightweight materials or precast elements are becoming more common as well, the latter saving construction waste. Efficiency-improving methods like these reduced cement use for the New York Freedom Tower by as much as 40%.
A second reduction strategy is to look at the potential to substitute cement and concrete with low-carbon and lightweight alternatives such as cross-laminated timber (CLT). Substituting concrete in one part of a building can have a snowball effect elsewhere: when lightweight materials are used, slabs and foundations can also be designed to support a smaller load. Studies reveal a carbon footprint reduction of about 40% when using CLT instead of steel or concrete for multi-story buildings.
2) Changing the rate at which we build
If we can extend the lifetime of existing buildings and infrastructure, we can reduce demand for new construction. There is growing momentum in favor of reusing and reinforcing the internal concrete structures of buildings, which can as much as double their lifespan. Enhanced sharing practices and efficient use of existing spaces can further reduce the need for new construction. When concrete ultimately reaches end-of-life, changes in decommissioning practices can reduce future cement demand.
A focus on reduction may seem like an obvious step for decarbonization, but strategies for the cement and concrete sector have so far relied heavily on supply-side technologies instead. In order to reduce demand, stakeholders such as architects, urban planners, landowners, constructors and general consumers need to come together in a collective effort. It is clear that this will not happen by itself: there is no financial incentive for the industry to promote demand-side intervention. Moreover, concrete and cement costs form only 10% of total spending in the construction sector, resulting in weak economic incentives on the demand side as well. We therefore need clear policy guidance and a stronger focus on material efficiency.
Short-term technological improvements
Next to reducing demand, it is also necessary to improve the sustainability of the supply chain of cement. Here’s where technology plays a key role: innovations complement and accelerate emission cuts on both the supply chain and demand side. The good news is that the options below are already in use or being tested today, which is promising for emission reduction in the short term.
Alternative combustion fuels
By changing the fuel used for heating the cement kiln, we can tackle one of the primary emission sources in production. This is not a new method: alternative fuels are already commonly used in the cement industry and include waste materials, scrap tires, and sewage sludge. In the EU, municipal solid waste and sewage sludge already accounted for 17% of the thermal energy needed for EU cement production in 2004. There are some considerations to keep in mind, however:
- The realized emission reduction is often only marginal — the substitution rate of alternative fuels is typically limited because certain chemicals, such as zinc, present in these fuels can impact the cement's hardening process. Most cases see a reduction between 1-5% with up to 18% in a few instances.
- Some alternative fuels contain materials like nitrogen or heavy metals. Co-processing in a kiln can therefore lead to higher emissions of non-CO2 pollutants.
Clinker substitution
Clinker is one of the principal components of cement. Producing this intermediary product accounts for about 90% of all cement-related emissions. In addition, cement producers can consider partially substituting the material with materials such as fly ash, metal slag or calcined clay, ‘bypassing’ the emissions that the calcination and fuel combustion stages would otherwise generate. This has the potential to save as much as 1.3 gigatonnes of annual CO2 emissions- if we tackle these conditions:
- A shift in manufacturing, which includes a massive expansion in the processing and use of a broader range of alternative materials would be needed.
- The alternative materials must be standardized by (inter)national policy, and included in cement standards.
- More investments in the research and development of alternative materials.
Terra CO2 is one company showing us how it can be done. Terra substitutes clinker by using a mix of silicate rocks, like granite, basalt, glacial flood gravel and clay-sand mixtures, which it estimates can result in 70% lower CO2 emissions compared to pure Portland cement.*
Carbon capture and storage
CO2 Capture Utilization and Storage (CCUS) technologies have the potential to significantly reduce CO2 emissions from both primary sources by capturing it before it enters the atmosphere — though we also see technologies focused on only capturing one type. This carbon can be reused or injected into the earth for permanent storage, for example in depleted oil and gas reservoirs.
While not all factories are suited for it, CCUS is on the horizon as several players in the industry are running pilots. To achieve net zero emissions by 2050, the industry will need to adopt CCUS at a much faster pace. A combination of direct and indirect incentives, regulatory enablement and risk management will be needed to tackle the challenges currently slowing down our journey there:
- The tech is still costly, which slows down the scaling of the technology. That said, CO2 pricing (like the EU ETS in Europe), while not expensive enough yet, will likely make a difference here, as it is creating a business case for CCUS.
- There is currently a bottleneck of storage locations. While we expect the demand for CO2 storage to increase, the pace of storage facility development needs to catch up.
- Companies are cautious about spending on CCUS project development without regulatory certainty, while policies that enable CCUS projects are complex and still evolving. One reason is that CCUS consists of many components, such as transport and storage networks and sub-surface monitoring. Combining these requires new collaborations and intensive coordination. Consequently, the various components have yet to be combined repeatedly at scale.
Injecting CO2 into concrete
Wait, did anyone say ‘bottleneck’? CO2 mixing may be the answer. It combines the superpowers of CCUS tech and concrete innovation in order to store captured CO2 in the concrete itself during the batching and mixing process. CarbonCure, one of our portfolio companies, is a pioneer in this promising technology.
The knife cuts both ways when it comes to CO2 emissions: CO2 can be sequestered in the concrete production process, reducing emissions by 5%, or even 25-30% with newer methods, preventing CO2 from reaching the atmosphere. Simultaneously, it makes the concrete it is injected in lighter, reducing the material footprint of the concrete. And it also strengthens the concrete it is injected in, reducing cement demand.
Software applications
Software start-ups are increasingly putting their efforts into helping the cement industry implement these short-term carbon footprint reduction measures.
AICRETE is one of these startups. The company combines data and AI with automation and extensive domain knowledge to develop new concrete mixtures. Structural engineers can now have their cake and eat it too: next to being more cost-effective, the mixtures are more sustainable, with a reduced carbon footprint of up to 35%.
Another company harvesting the power of AI to reduce costs and emissions is Carbon Re. The company has developed software for industrial decarbonization, with the aim of uncovering energy efficiencies and reducing costs. Their product Delta Zero Cement optimizes the cement's pre-heater and kiln process stages, leading to cost savings and a fuel usage emission reduction of up to 20%.
Long-term technological improvements
New developments are underway to produce the next generation of cement, although they may need more time and investment to get there compared to the previously mentioned startups.
Electrolysis and hydrogen application
Sublime Systems skips the calcination process (responsible for half of cement CO2 emission) using alternative calcium sources. It uses an electrochemical process that turns abundantly available non-carbonate rocks and centuries of industrial waste into calcium sources that don’t release CO2 when decomposed. The rest of its blending process occurs at ambient temperatures, meaning it doesn’t involve any fossil-fuel-burning, high-temperature kilns.
Nature-based solutions
There are also cement innovators who draw from the power of nature to create next-generation cement. Biomason removes heat from the discussion by eliminating the need for a kiln process. The startup uses a bioreactor to pull limestone, microorganisms, water and carbohydrate feed together to create a natural cementitious material, removing 75% of emissions compared to ordinary Portland cement.
In line with Biomason, Minus Materials uses nature-based solutions to decarbonize the cement industry. The company grows carbon-negative, bio-renewable limestone using calcifying microalgae. The limestone can be directly used in the production process as it is, and it only releases CO2 that was previously sequestered from the atmosphere during the algae’s lifetime, yielding a 60% CO2 emission reduction.
Innovating the traditional process
Brimstone has developed a new process to make industry-standard cement using basalt and other calcium-bearing silicate rocks instead of limestone.* These replacement rocks are rich in calcium oxide, a key ingredient in cement-making, but they don’t contain any carbon atoms. Its cement-making process produces a magnesium compound as a byproduct, one that binds with carbon dioxide to remove it from the atmosphere permanently.
Paving the way for net zero cement
There has been an impressive amount of new ideas and technological innovation. However, this progress continues to be has been hindered by these key factors:
- A critical lack of funding remains a hurdle for scaling capital-intensive cement startups, limiting their ability to bring their innovations to market. However, the next two factors may be even more important.
- Long regulatory approval timelines for new production methods and cement types for structural use slow down innovative cement technologies from getting to market. Shifting from recipe-based standards to performance-based ones, allowing the uptake of all low-carbon cement solutions on the market can help accelerate the process.
- The conservative cement sector is challenging to disrupt due to high barriers to entry, low margins, and powerful incumbents with huge amounts of embedded infrastructure and supply chains. To get to net zero, we need incumbents to innovate themselves or acquire innovative tech (buying the startups/scaleups) and bring them into their embedded infrastructure and supply chains.
Building upon the positives
Governments are making important progress in decarbonizing cement. The US Inflation Reduction Act and the EU ETS, which increases the cost of carbon, provide financial incentives for the cement industry to innovate and reduce emissions. EU cement companies are already updating their commercial strategies for recycled and low-carbon cement products.*
China, accounting for more than half of the world’s cement production, launched Carbon Peak Implementation Plan for Building Materials Industry with the plan of carbon emissions peaking before 2030 and lowering through the deployment of low-carbon materials and technology. One promising international campaign to reduce carbon emissions in built projects is the Industrial Deep Decarbonisation Initiative (IDDI), coordinated by the United Nations Industrial Development Organization (UNIDO). The IDDI hopes to obtain commitments from at least 10 countries to begin to adopt low-carbon steel and concrete procurement policies within the next three years.
More of the private sector has also started to move under the First Movers Coalition, which mobilizes companies to decarbonize hard-to-abate sectors (including cement) by committing to purchase from zero-carbon suppliers.
As you can see, the blueprint to net zero requires multiple key stakeholders. But if governments, corporates and investors continue to work together, there's a pathway to overcome the cement industry’s emissions and solve this climate challenge.
Did you find this article insightful? Let us know in the chatbot or connect with Liza, our Co-Founder and Head of Impact, on LinkedIn! If you are interested in investing in the next generation of cement, have a look at our investment opportunities.